Bulk Storage and Elevator System for Food Processing
Jump to: System Specifications || Quote Request Form
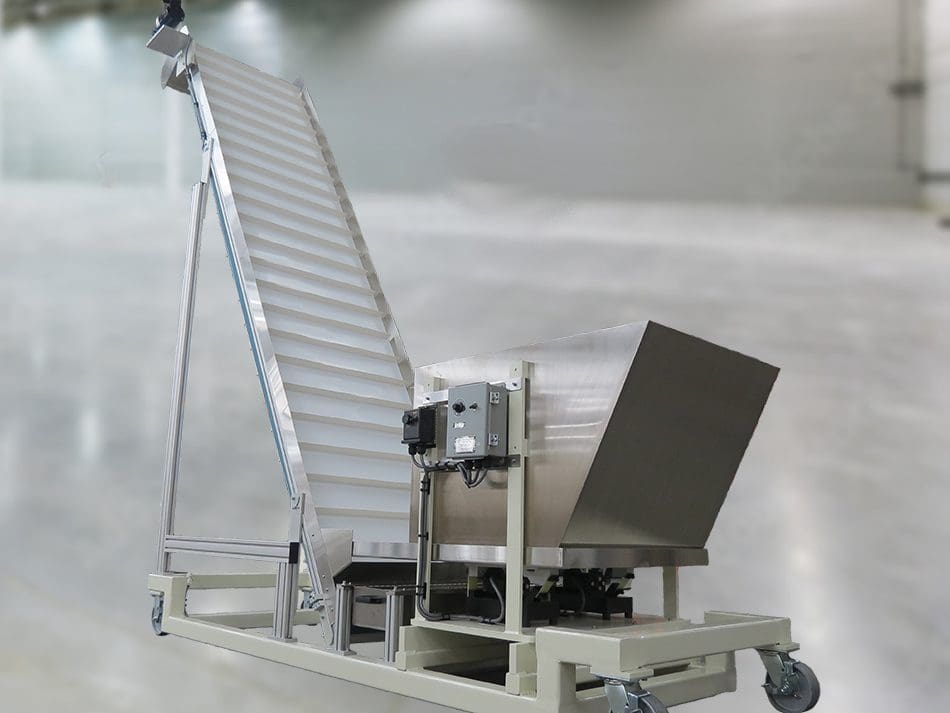
This system was designed for a food manufacturer who needed to move a whole-grain snack product to a packaging operation, which required the product to be delivered 10′ off the floor. The manufacturer needed bulk product storage at floor level and a way to remove as much small and broken pieces of product as possible before moving into the packaging operation.
System specifications
- Conveyor belt speed: 9 – 32 feet per minute, variable speed.
- Input voltage: 120V, 60 Hz.
- Incline belt conveyor:
- Auto-Kinetics Model 55 Heavy-Duty belt conveyor, 800mm wide x 149″ long.
- FDA-approved belt with 40mm high cleats on 6″ centers.
- Custom end drive module, 1/4 HP motor, 130V DC.
- Polished stainless steel side rails, entrance bin and exit chute.
- Extruded aluminum incline stands mounted to system frame.
- Bulk supply hopper:
- Custom polished stainless steel 12 cu. ft. bin.
- Custom polished stainless steel 30″ wide vibratory tray with perforated discharge area for small particle removal
- Powered by two vibratory hopper drivers.
- Particle collection system:
- Polished stainless steel tray under perforated supply hopper discharge tray.
- Tray slides out of frame by hand for easy cleaning.
- System frame:
- 3″ steel tubing, painted.
- Casters with FDA-approved wheels for portability.
- Controls provided:
- PF-1R for bulk storage hopper.
- PF-111 DCPM for incline belt conveyor.
Downloads
Performance Feeders Tri-Fold Brochure
Model 55 Belt Conveyor Product Card