The Advanced Process
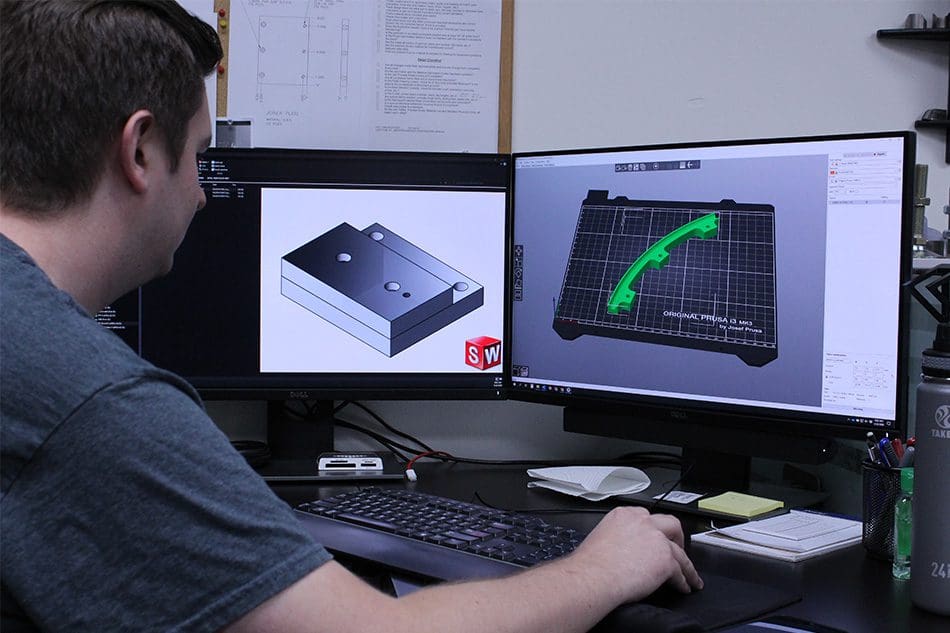
Collaboration between Designers and Feeder Tooling Technicians ensure a blend of proven tooling technique and manufacturing design protocol
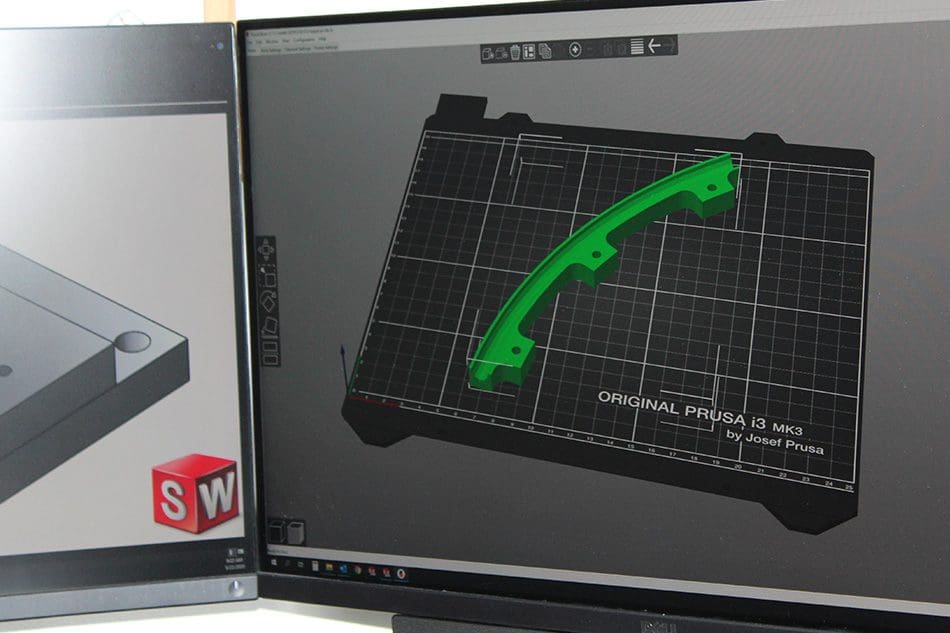
Designers employ 3D CAD software to bring the tooling concept into a 3D viewable form
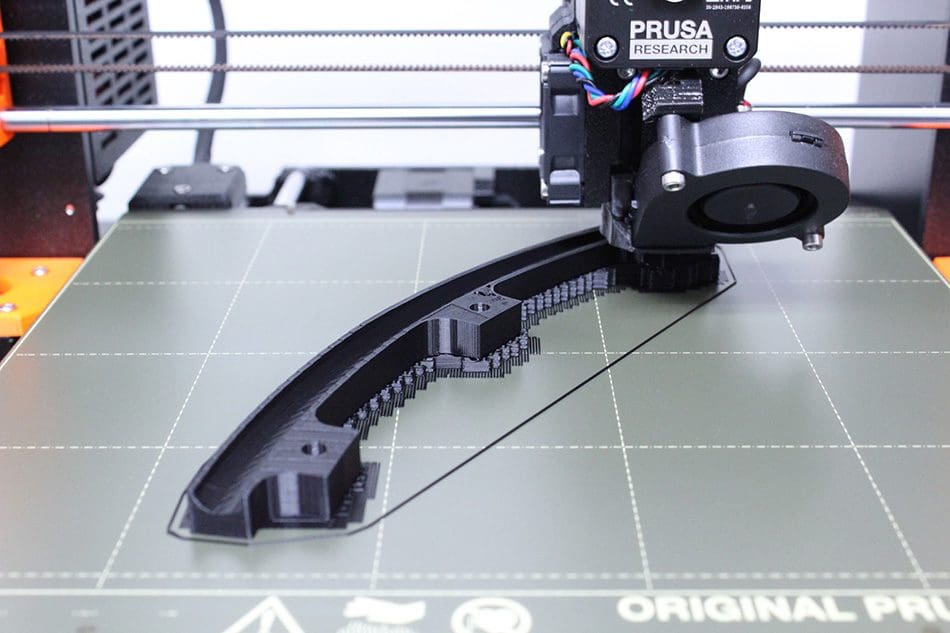
The 3D model is uploaded to the 3D printing device
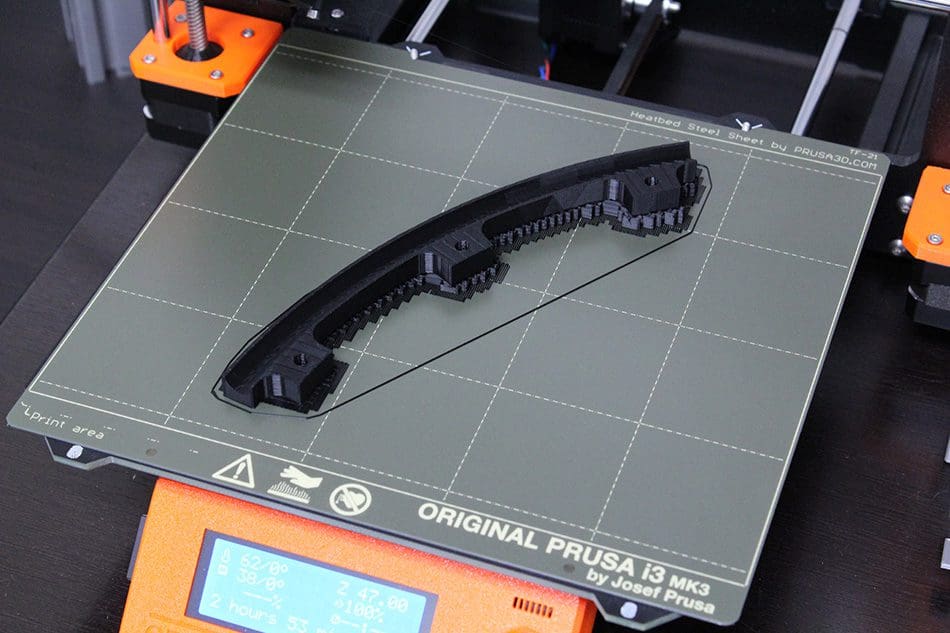
Various plastic materials can be utilized to create a replica of the 3D model depending on how the tooling will be used.
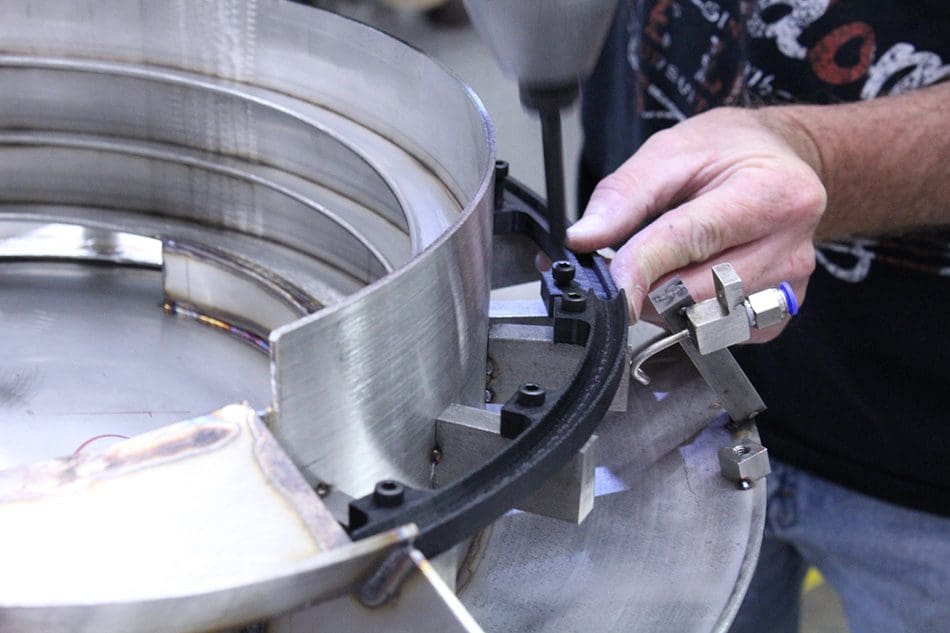
The finished printed tooling can then be mounted to the feed system to prove the concept.
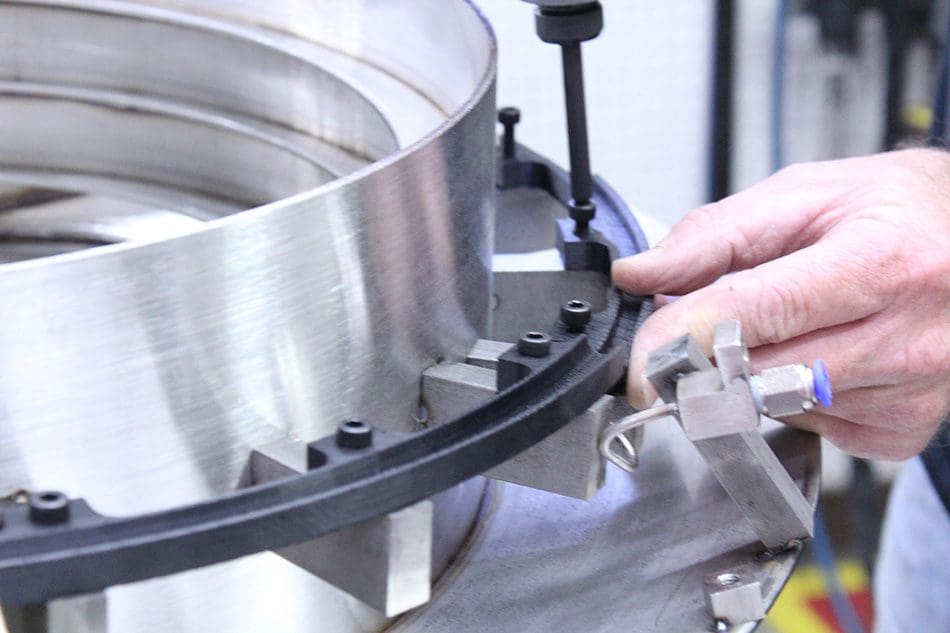
The plastic printed model is durable enough for testing and minor modifications can be made by the Tooling Technician to assist in finalizing its design
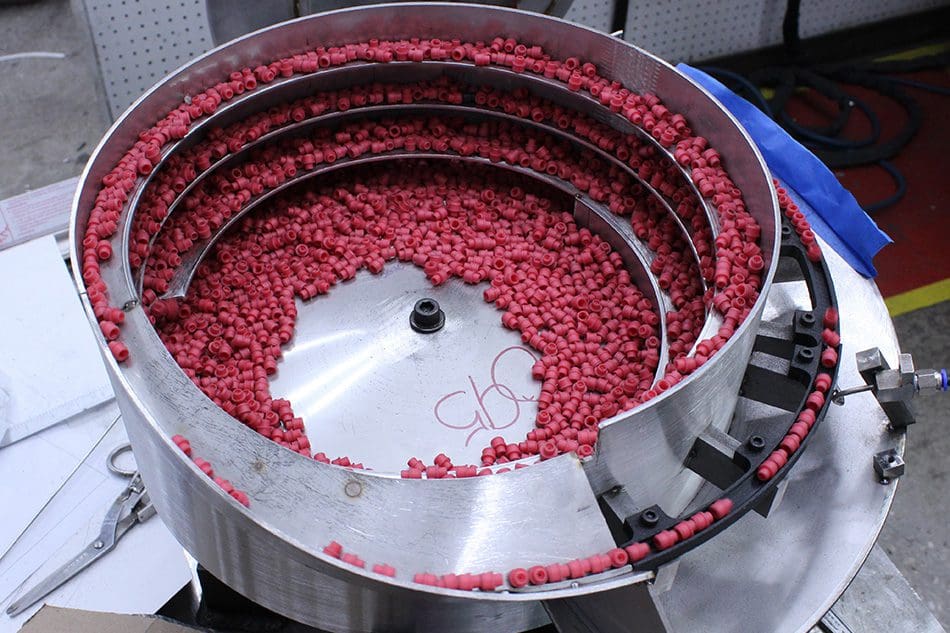
Continued testing is undergone to confirm final tooling design
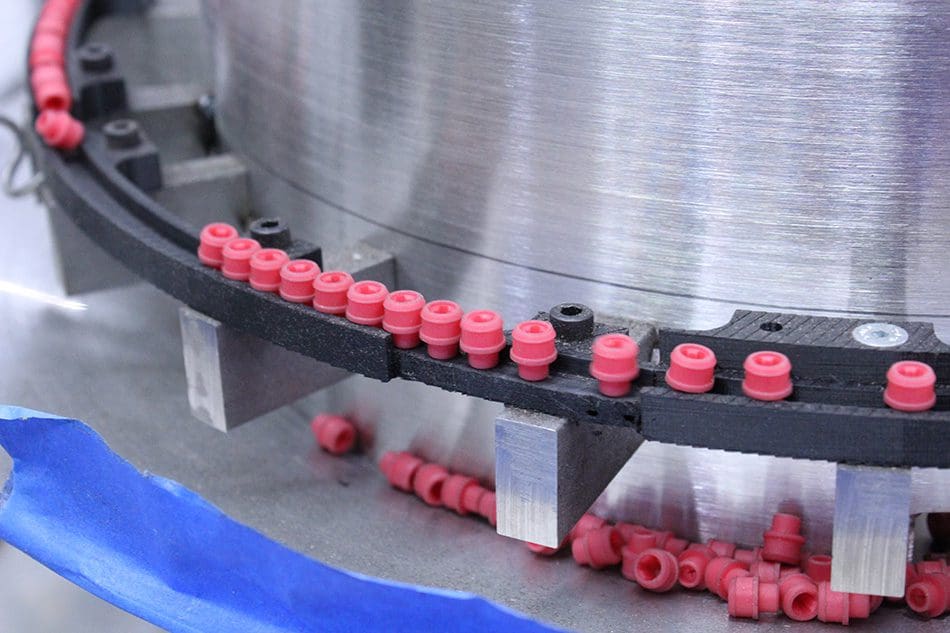
During this process, the time and material saved by 3D printing means that any major changes to the tooling can be accommodated quickly, new tooling can be printed, and testing can continue within hours instead of days.
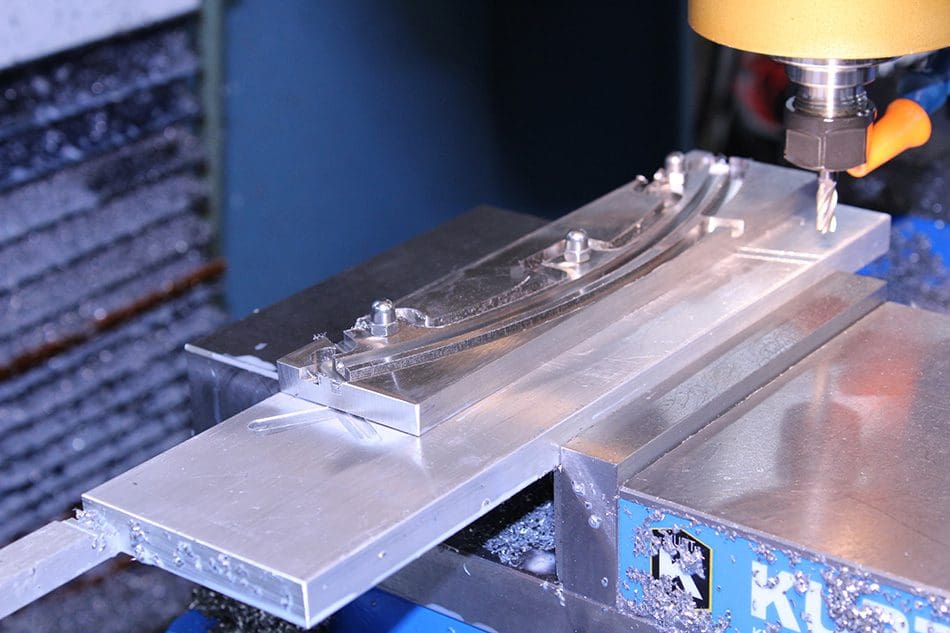
Advanced CNC machines coupled with highly skilled machinists allow for the final tooling components to be created even when complex geometries are involved
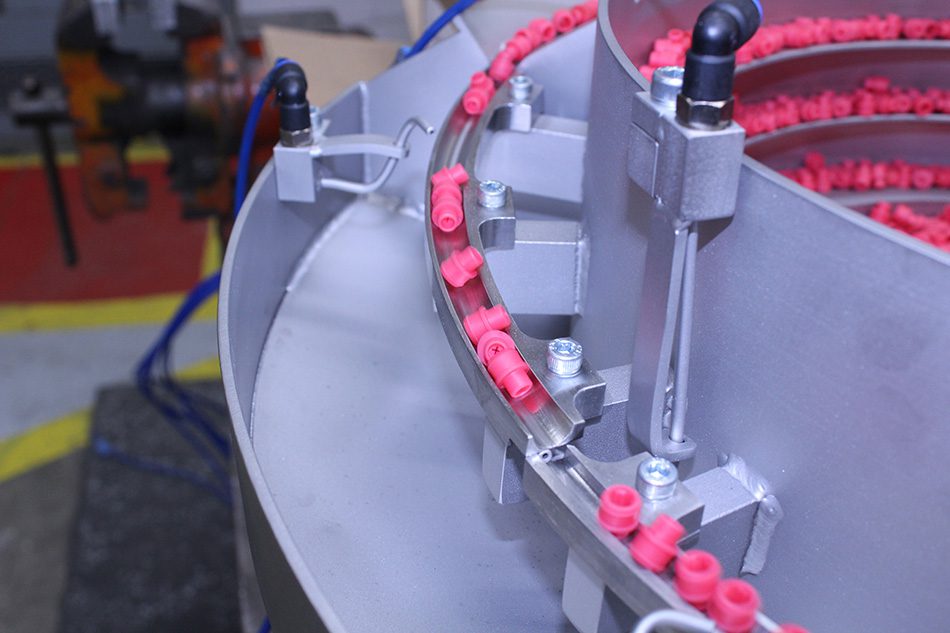
This results in an accurate and repeatable tooling process which can save time and money on reproduced projects or allows for a feed system to be repurposed for a similar part which in the past may have required an entirely new feeder be built, but in this case new machined components can be inserted and replaced.
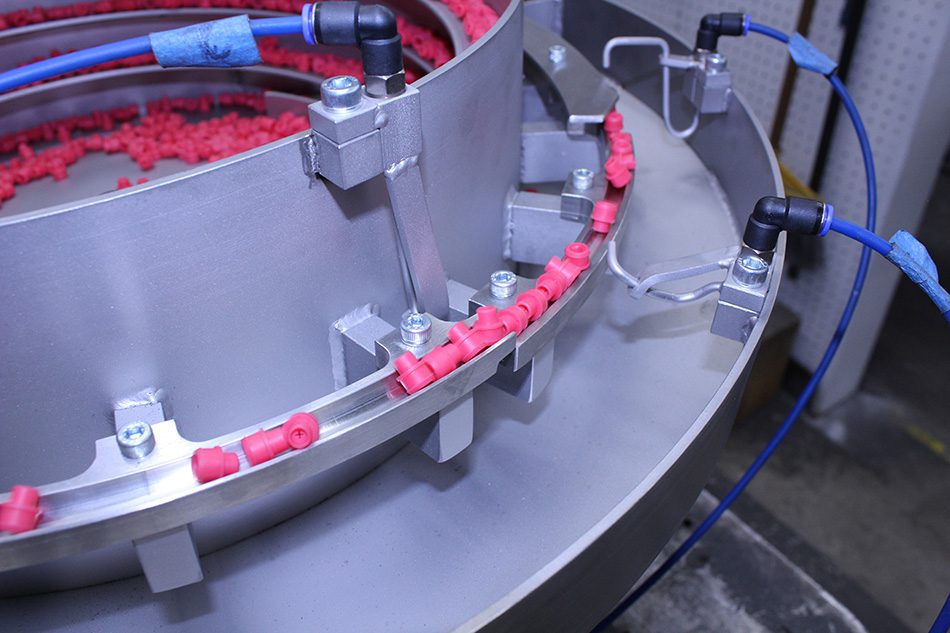