Belt Conveyor System with Airlock Chamber for Moving Product Through a Cleanroom for a Medical Packaging Operation
Jump to: System Specifications || Quote Request Form|| Download Flier
We were approached by a medical device manufacturer who needed a solution for moving empty packages from a warehouse into a cleanroom for packaging with product, then moving the full packages back into the warehouse for storage and shipment. They required continual movement of product between the warehouse and the cleanroom while maintaining the integrity of the cleanroom environment.
We designed two custom belt conveyor systems: One for transferring empty packages into the cleanroom, and one for transferring loaded packages out of the cleanroom. Each conveyor system included 3 custom belt conveyors and a custom airlock enclosure that isolated the product moving between the warehouse and the cleanroom.
View these short videos that demonstrate the operation of the airlock chamber as it automatically moves packages between a warehouse and a cleanroom without allowing contaminants into the cleanroom.
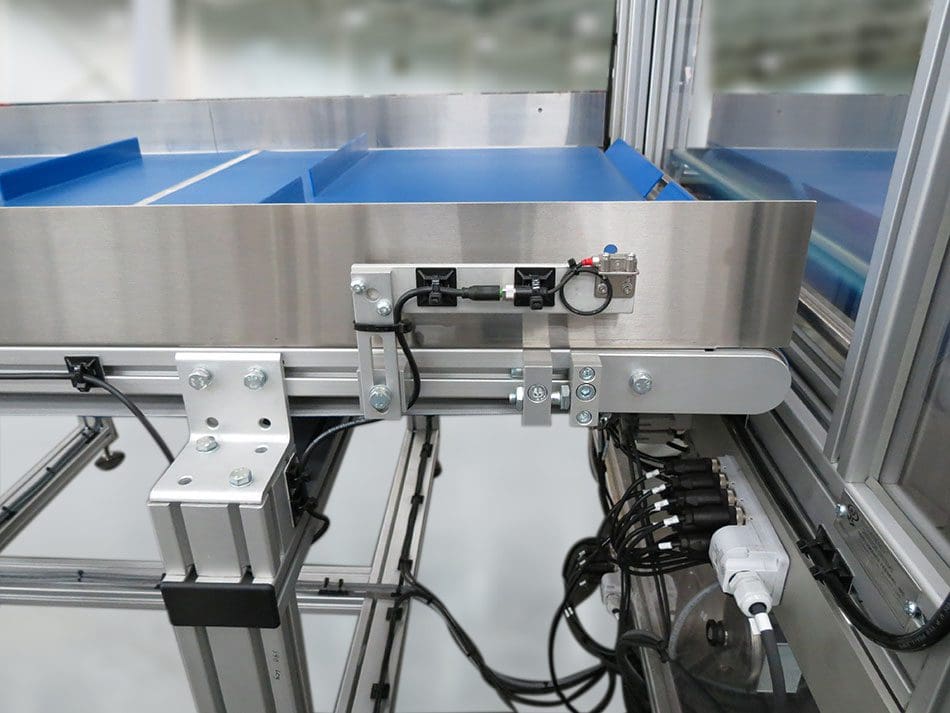
While the conveyor systems were designed to be loaded and unloaded by operators at each end, the movement of product through the systems was controlled by position sensors wired to a programmable control system.
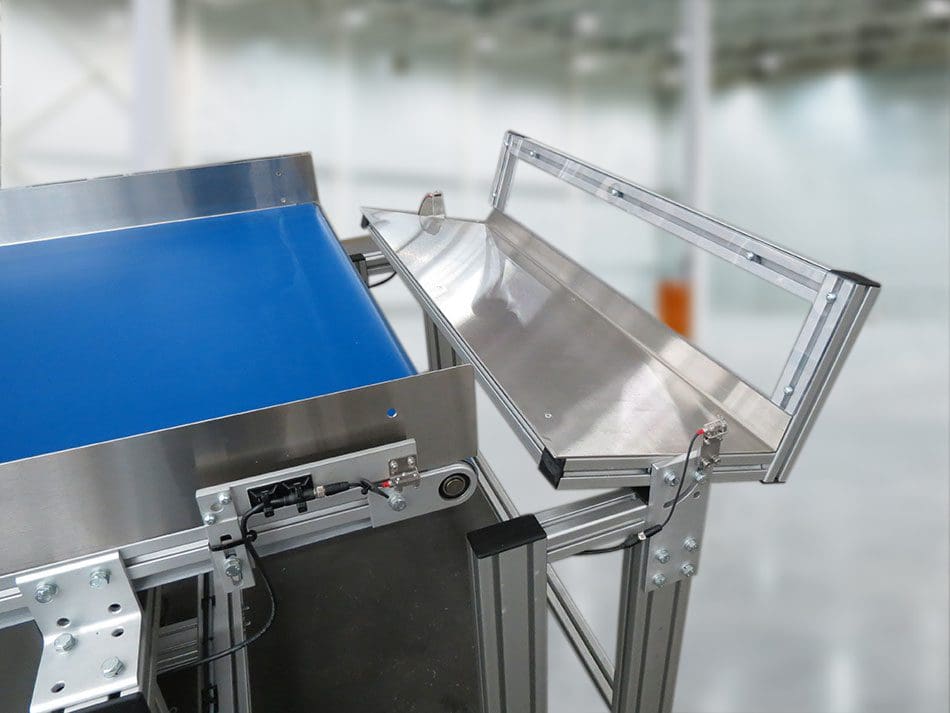
Empty packages transferred into the cleanroom dropped onto this table to wait for operators to pick them up. Position sensors on the table sensed when the table was empty, automatically activating the conveyor system to supply more packages.
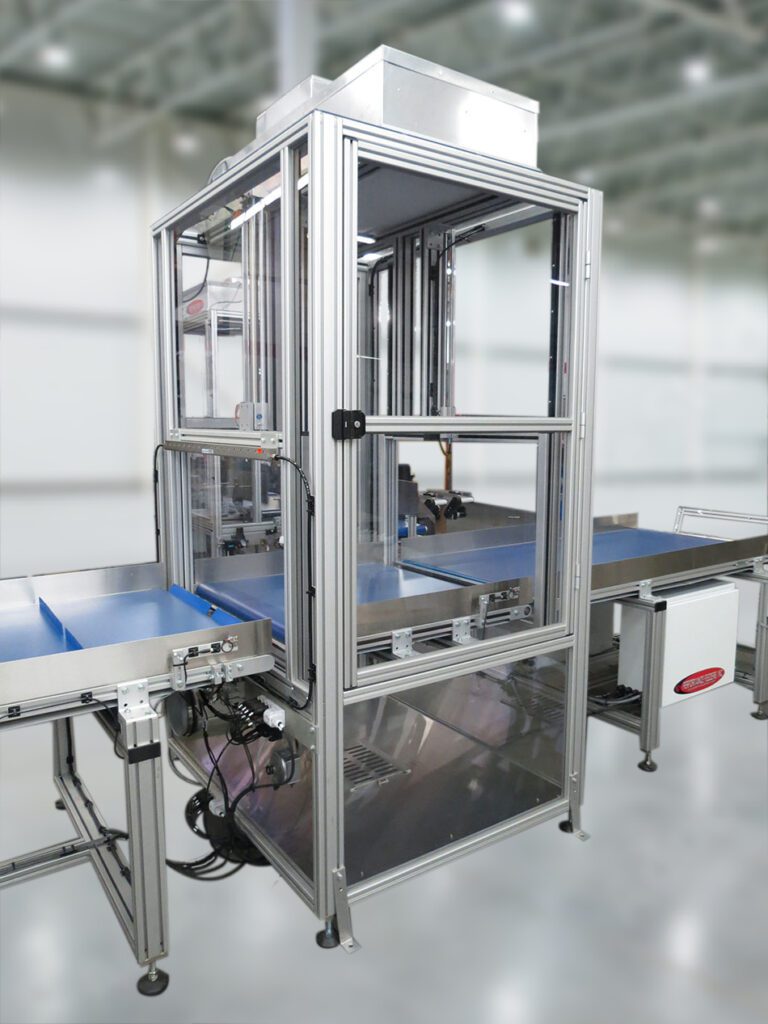
The airlock enclosures were custom-designed to prevent contaminated air from entering the cleanroom. Only one door could be open at a time. Each enclosure had an air knife over the entrance door that activated when that door was opened, preventing air from entering or exiting the enclosure. Before product was allowed to exit an enclosure, the enclosure was pressurized with filtered air to purge out any contaminants that may have entered.
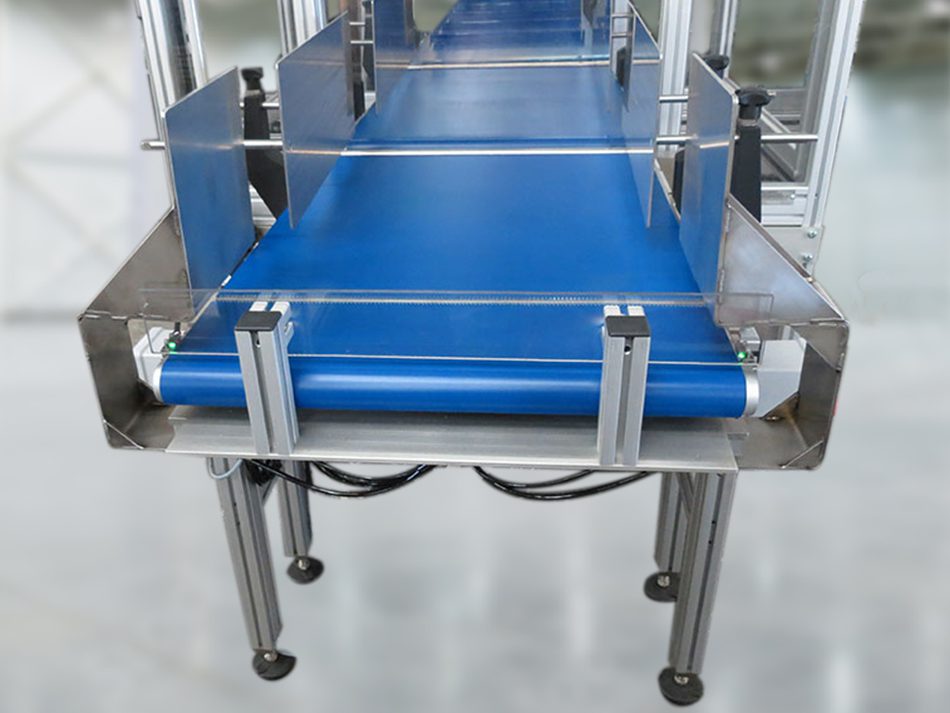
Full packages transferred out to the warehouse went into this foot-operated compression mechanism so the operator could compact the packages prior to removing them for storage.
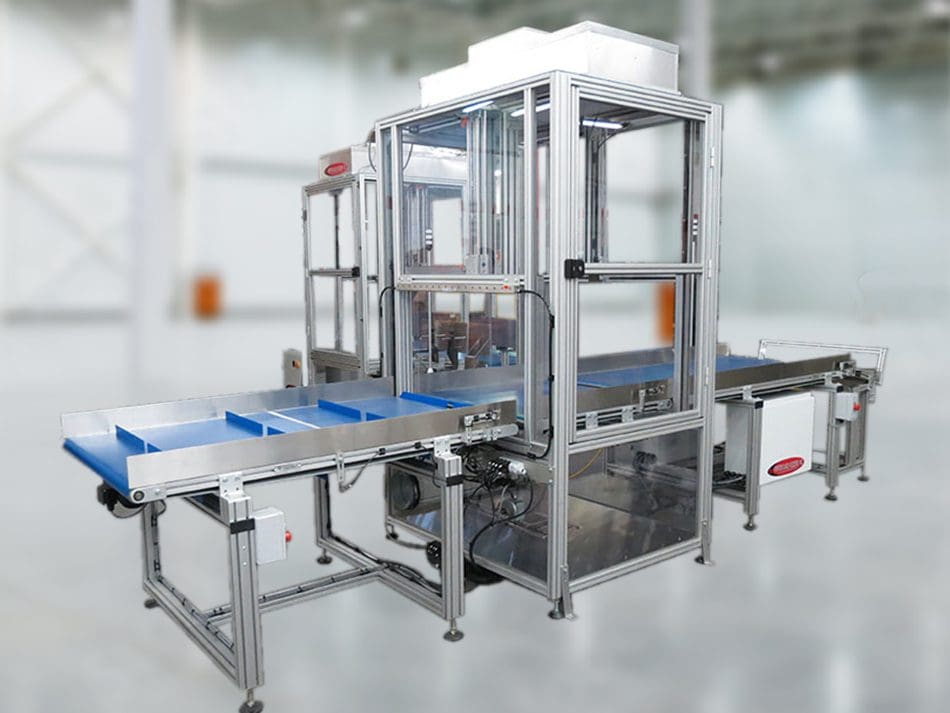
Custom Conveyor System specifications
- Input voltage: 220V, 60 Hz.
- General conveyor specifications:
- Anodized aluminum and stainless steel construction.
- Belts:
- FDA-approved urethane belts.
- Cleats on conveyors feeding into airlock enclosures to maintain proper package spacing.
- Drives: 3/8 HP inverter-duty motors, 230V 3 phase with AC variable speed motor controllers.
- Belt speed: 30 feet per minute.
- Infeed conveyor system (moves empty packages into cleanroom):
- Load conveyor (warehouse side):
- Advance buttons on both sides of entrance for operator to initiate indexing after conveyor is loaded with empty packages.
- Emergency stop buttons on both sides of entrance.
- Photoelectric sensor at exit to detect when packages are position to move into airlock enclosure.
- Beacon light to alert operator of various system operating conditions.
- Airlock conveyor (moves product through airlock enclosure): Photoelectric sensor at exit to detect when packages are ready to move out of airlock enclosure.
- Unload conveyor (cleanroom side):
- Emergency stop buttons on both sides at exit.
- Discharge table at exit end of conveyor for operator to unload packages.
- Photoelectric sensors at conveyor exit and on discharge table to sense whether packages are present.
- Beacon light to alert operator of various system operating conditions.
- Load conveyor (warehouse side):
- Outfeed conveyor system (moves loaded packages out of cleanroom):
- Load conveyor (cleanroom side):
- Adjustable stainless steel side rails.
- Advance buttons on both sides of entrance for operator to initiate indexing after conveyor is loaded with packages.
- Emergency stop buttons on both sides of entrance.
- Photoelectric sensor at exit to detect when packages are position to move into airlock enclosure.
- Beacon light to alert operator of various system operating conditions.
- Airlock conveyor (moves product through airlock enclosure):
- Adjustable stainless steel side rails.
- Photoelectric sensor at exit to detect when packages are ready to move out of airlock enclosure.
- Unload conveyor (cleanroom side):
- Adjustable stainless steel side rails.
- Emergency stop buttons on both sides at exit.
- Compression mechanism, operated by a foot pedal, at conveyor exit for operator to compress packages before unloading from conveyor.
- Photoelectric sensor at exit to detect when packages are in position in compression mechanism.
- Beacon light to alert operator of various system operating conditions.
- Load conveyor (cleanroom side):
- Airlock enclosures:
- Anodized aluminum and stainless steel construction with Lexan and stainless steel panels.
- Completely sealed with automated air pressurization system that includes HEPA filter and automatic venting.
- Air knife mounted above entry door that minimizes air entering or exiting the enclosure when entry door is open.
- External wall seal to seal against warehouse wall.
- Powered entry and exit doors.
- Manual side maintenance doors.
Downloads
Performance Feeders Tri-Fold Brochure
Model 55 Belt Conveyor Product Card