Vibratory Feeder With Integrated Vision System Orients Parts Based On Internal Features
Jump to: System Specifications || Quote Request Form || Download Flier
This vibratory feed system was designed to feed a metal washer into a machine assembling a consumer product. While flat, round parts like washers are normally easy to feed, this part had a small indentation on one side that needed to be oriented facing down.

A vision system was mounted over the vibratory bowl tooling right before the discharge to check the top to bottom orientation. If an improperly oriented part was detected, the PLC that controlled the vision system activated an air jet which blew the part off the track and back into the bowl feeder for recirculation.
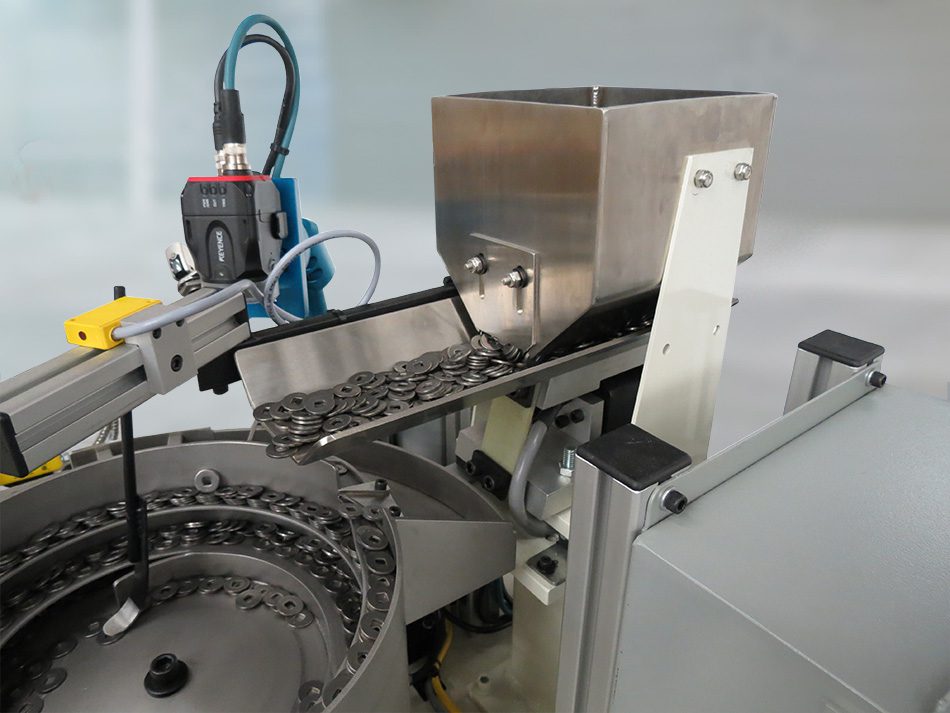
A bulk supply hopper with a stainless steel bin and tray provided 1/4 cu. ft. of bulk parts storage with automatic metering of parts into the vibratory bowl.
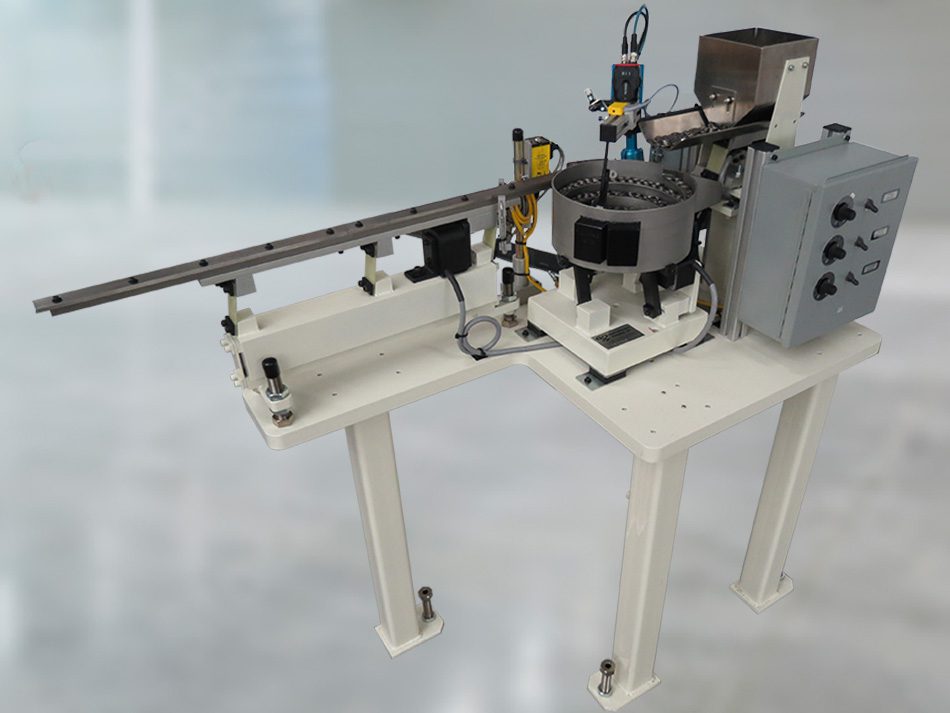
System specifications
- Feed Rate: 25 parts per minute.
- Input voltage: 120V, 60 Hz.
- Vibratory bowl:
- 10″ basic diameter.
- Counterclockwise rotation.
- Bead blasted stainless steel construction.
- Vibratory straight line track:
- 36″ long.
- Stainless steel construction.
- 3-spring vibratory inline driver.
- Bulk supply hopper:
- 1/4 cu. ft. capacity with table mount.
- Stainless steel bin and tray.
- Vision system: Keyence camera with proximity sensor and PLC.
- Controls: Performance Feeders PF-3R.
- Mounting surface: 1.25″ thick steel table with 4 legs and leveling screws.
- Sensors and valves provided:
- Photoelectric sensor on straight line track monitoring part level in track. When track is full, the bowl is turned off to prevent parts from backing up into the bowl.
- Proximity sensor on hopper monitoring parts level in bowl, turning on hopper when parts are needed.
- Proximity sensor on bowl feeder in camera area, sensing part in place for vision inspection.
- Solenoid valve package with regulator and flow controls for air jets.
Downloads
Performance Feeders Tri-Fold Brochure
Vibratory Feeder Bi-Fold Brochure
Vibratory Feeder Rack Card