Container Unscrambler for Medical Packaging
Jump to: System Specifications || Quote Request Form
Our customer presented us a bottle with a geometric shape that was ideal for our standard feeding techniques. However, two challenges were presented during the feeding process.
The first challenge was that the plastic material generated electrical static as the parts moved and rubbed together creating excessive static build up.
The plastic material was also extremely tacky, inhibiting free movement of the parts through the system or through the feeder tooling which affected the system feed rate. The initial solution was to increase the number of air jets used to assist in moving the part through the tooling via compressed air, but this only caused volatile movement which further complicated the tooling process and elevated considerably the production cost of the system. The feed rates required were supposed to be more than 250 ppm and we were initially only realizing 90 ppm.
When producing standard feeder tooling the bowl builder relies on a part’s geometry and center of gravity to influence the part into the positions needed to achieve the final orientation required by the customer.
In this application we were expecting a 75-80% loading ratio (the number of V-Groove pockets to be filled by a part in one rotation) and what was realized was initially less than 50% due to the unique material characteristics that created high friction and significantly reduced the product flow and movement.
We needed to design out the aperiodic nature of feeder tooling and design tooling and processes which guaranteed 100% of V-Groove pockets were filled and every product was oriented regardless of its position entering the system.
The centrifugal solution you see below provided a 100% load ratio, resulting in higher feed rates at lower rpms and allowing for a smaller system footprint which saved manufacturing floor space.
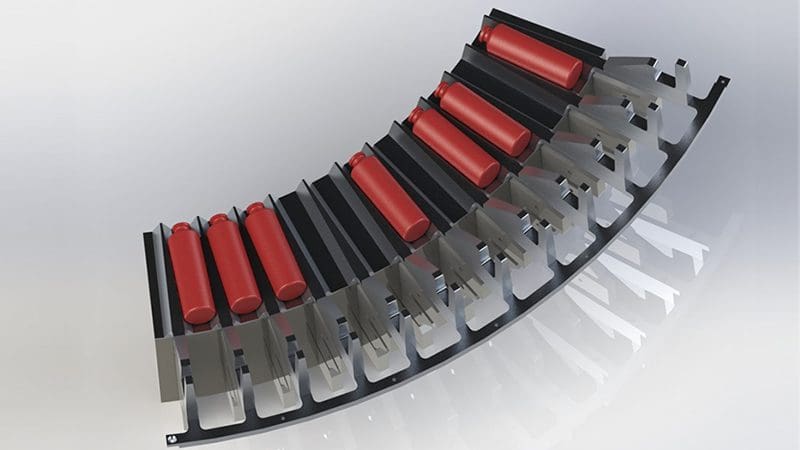
Traditional feeding solutions: In the standard scallop feeder design, parts start in a horizontal position and a large outer disc with “V” shaped pockets are machined radially with each groove pointing toward the disc’s center. A second rotating disc in the center of the equipment moves the parts via centrifugal force to the outside edge and onto the grooved disc while trying to rotate the part 90 degrees and settle into a V-shaped pocket
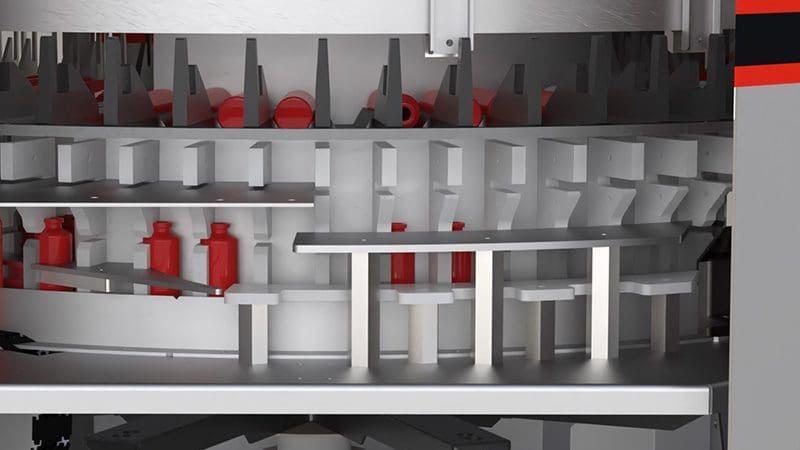
Upright and oriented product passed through a mechanical inspection which mechanically profiled the product to determine if a part was in the correct attitude.
If the product was found to be in the wrong orientation it was released through the lower floor and out the reject chute.
If the product was found to be in the wrong orientation it was released through the lower floor and out the reject chute.
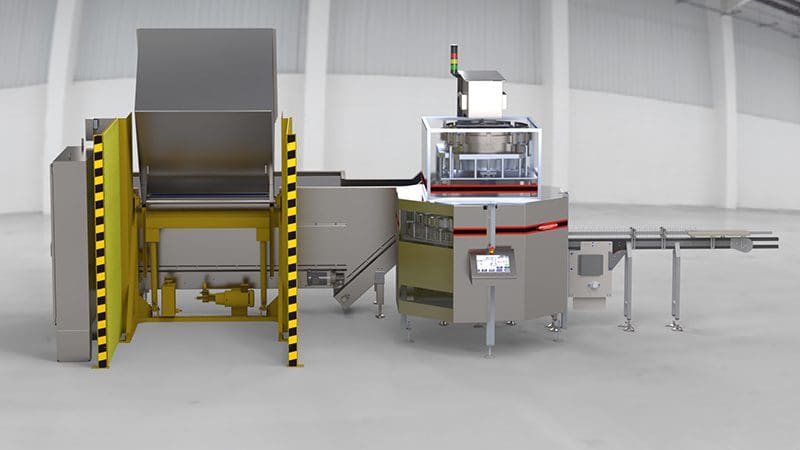
Specifications
With our track machining capabilities, our vibratory feed system tracking components are constructed on our new ProtoTrak CNC’s in longer lengths to reduce seams for longevity and durability.
Feed rate: 250 parts per minute.
Input voltage: 220V, 60 Hz.
Complete stainless-steel build with clean room design in mind to reduce/eliminate particle build up on machine surfaces. Stainless steel hex head fasteners used where possible
Automatic Box Dumper:
- Capable of lifting and dumping 48” x 48” x 48” Gaylord boxes.
- Ground entry loading
- Auto / Manual tilt controls
- Low / Mid / High limit switches for programmable run sequences
- 135-degree bucket rotation
- Hydraulic pump and cylinders.
Bulk Product Storage and Delivery:
- Custom 80 cu ft storage capacity hopper.
- PFI Vertical cleated conveyor to lift product out of hopper.
- Low / Mid / High level sensors in hopper.
- Qty (2) 1/4 HP 220 VAC motors.
Vertical Elevator:
- PFI custom elevator carries product to the bottle orienting equipment.
- Low / High bin level sensors.
- Mounted 3 color stack light with alarm.
- ¼ HP 220 VAC Motor.
Centrifugal Orienting Equipment :
- 30″ diameter upper pre-orienting spinner.
- FDA compliant product contact surfaces.
- Air Assisted gravity tracking.
- Lower, rotating, orienting platform with mechanical cam plates.
- Mechanical torque limiting and air clutch for safety and tooling protection.
- Clockwise rotation.
- Mechanical upside-down bottle reject.
- Qty (2) 1/4 HP 220 VAC motors.
Exiting Conveyor:
- 10-foot-long tabletop chain.
- Stainless steel construction.
- Side guides and bottle transfer plates.
- Low / Mid / High level product sensors
- ¼ HP 220 VAC Motor.
Controls:
- Performance Feeders custom Allen Bradley control system with HMI.
- Ethernet capable
- Allen Bradley PowerFlex drives.
- Integrated safety circuit
- Operates automatically on demand.
Downloads
Performance Feeders Tri-Fold Brochure
Container Unscrambler Brochure