Vibratory Feeder Bowl System with Center Discharge
Jump to: System Specifications || Quote Request Form
This vibratory parts feeding system was designed to feed two sizes of a part used in air conditioner desiccant systems. The simple cylindrical shape of the parts allowed the use of a “cascade” type bowl feeder, where all part orientation is performed within the inside diameter of the bowl. This eliminated tooling construction on the outside of the bowl, which along with the right-angle discharge into the vibratory track, resulted in a compact vibratory feed system that met our customer’s space requirements.
This short video demonstrates each size part running through the vibratory feeder and the tooling changeover procedure to prepare the feed system to feed the different sized part.
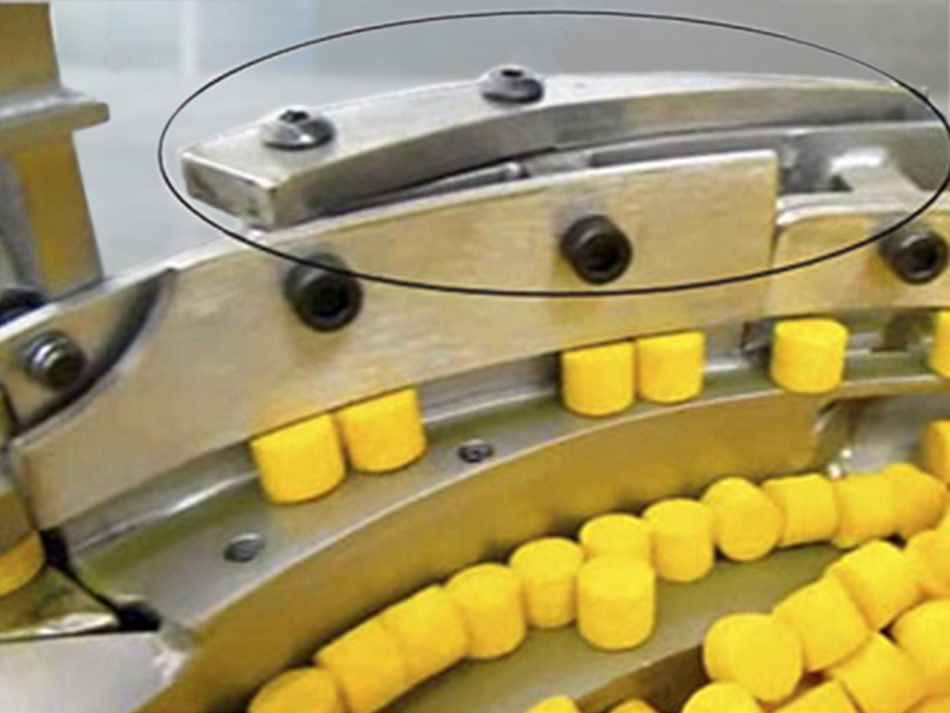
This photo shows the confinement (circled) bolted to a storage location when the system is running the larger diameter part.
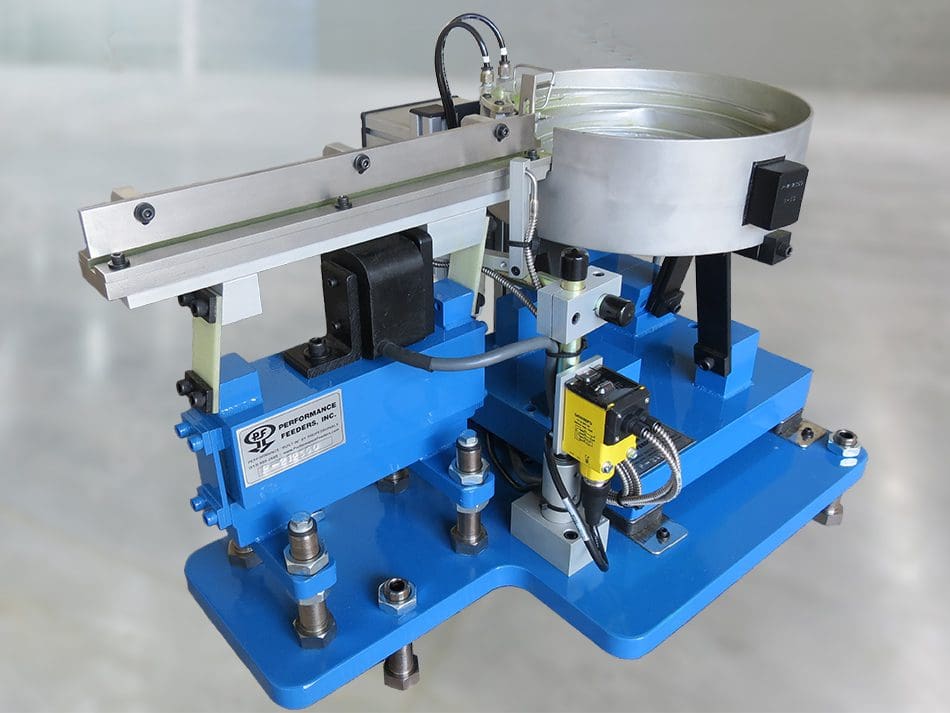
System specifications
- Feed rate: 25 parts per minute.
- Vibratory bowl:
- 12″ diameter cascade-style bowl.
- Stainless steel construction.
- Vibratory straight line track:
- Stainless steel construction.
- 15″ long.
- 2-spring vibratory inline driver.
- Controls: Reovib variable-frequency vibratory feeder controller.
- Mounting surface: 1″ thick steel plate with leveling screws.
- Sensors provided: Photoelectric sensor on straight line track monitoring part level in track. When track is full, the bowl is turned off to prevent parts from backing up into the bowl.
Downloads
Performance Feeders Tri-Fold Brochure
Vibratory Feeder BiFold Brochure
Vibratory Feeder Rack Card