Space Saving Vibratory Floating Mandrel Feed System Feeds Thin Metallic Washers
Jump to: System Specifications || Quote Request Form
This system was designed for a consumer products manufacturer to feed two types of washers: A wavy spring washer and a fiber washer. Vibratory bowl feeders were used to orient both parts, and the feed systems were mounted on a common table to save space and cost.
This short video demonstrates the discharge from the bowl feeder. The end of the mandrel extends into the bowl, where a cam tips the parts over and onto the mandrel so the parts are oriented face-to-face. Parts that miss the mandrel are recirculated through the bowl.
Because the mandrel was held in place by the parts inside the entrance and discharge retention blocks, photoelectric sensors were provided at both ends of the mandrel to ensure that the parts stack did not drop below the retention blocks. The sensor at the mandrel entrance, which was mounted above the retention block, turned on the bowl feeder when the part level dropped below the sensor. The sensor at the mandrel discharge, mounted just below the magnets, turned on the inline driver when the part level dropped below the sensor.
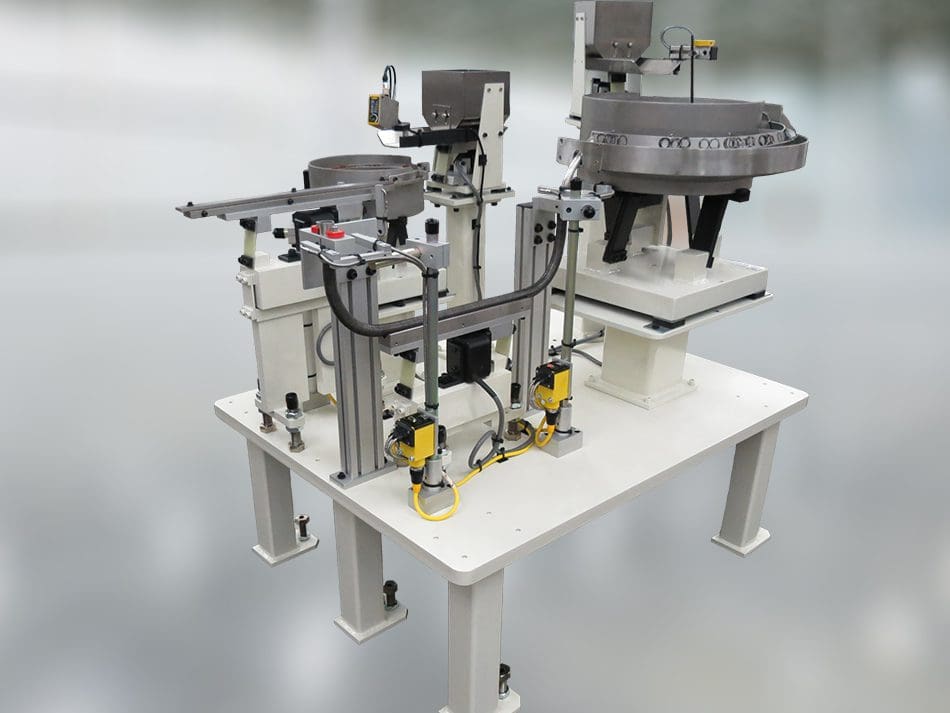
System Specifications
- Feed rate: 25 parts per minute
- Input voltage: 220V, 60 Hz.
- Vibratory feed system for spring washer:
- Vibratory bowl:
- 15″ basic diameter.
- Clockwise rotation.
- Bead blasted stainless steel construction.
- Vibratory floating mandrel:
- Stainless steel construction.
- 2-spring vibratory inline driver.
- The mandrel is pre-loaded with parts, rests on top of the inline driver and is held in place by retention blocks at either end.
- Bulk supply hopper:
- 1/2 cu. ft. capacity with table mount.
- Stainless steel bin and tray.
- Vibratory hopper tray.
- Controls:
- PF-3R modified for mandrel sensors.
- Sensors provided:
- Photoelectric sensor at mandrel entrance controlling part level at the mandrel entrance, turning on the bowl when the part level drops below the sensor.
- Photoelectric sensor at mandrel discharge controlling part level at the customer pickup point, turning on the inline driver when the part level drops below the sensor.
- Proximity sensor on hopper monitoring parts level in bowl, turning on hopper when parts are needed.
- Vibratory bowl:
- Vibratory feed system for fiber washer:
- Vibratory bowl:
- 10″ basic diameter.
- Clockwise rotation.
- Bead blasted stainless steel construction.
- Inside tooling design without return pan.
- Vibratory straight line track:
- Stainless steel construction.
- 18″ long
- 2-spring vibratory inline driver.
- Bulk supply hopper:
- 1/4 cu. ft. capacity with table mount.
- Stainless steel bin and tray.
- Vibratory hopper tray.
- Controls: PF-3R
- Vibratory bowl:
- Sensors provided:
- Photoelectric sensor on straight line track monitoring part level in track. When track is full, the bowl is turned off to prevent parts from backing up into the bowl.
- Proximity sensor on hopper monitoring parts level in bowl, turning on hopper when parts are needed.
- Mounting surface: 1.25″ thick steel plate with 6 legs.
Downloads
Performance Feeders Tri-Fold Brochure
Vibratory Feeder Bi-Fold Brochure
Vibratory Feeder Rack Card