Conveyor Belt System Feeds Parts Using Optical Inspection
Jump to: System Specifications || Quote Request Form
This custom conveyor system was retro-fitted to a vibratory feeder bowl to accommodate a part change that required a secondary inspection operation. The system consisted of a pair of Auto-Kinetics belt conveyors with custom tooling to maintain part orientation, and a 3-position shuttle mechanism between the conveyors.
This short video demonstrates a part in the shuttle after the escapement finger has lowered, allowing camera to view and inspect the part.
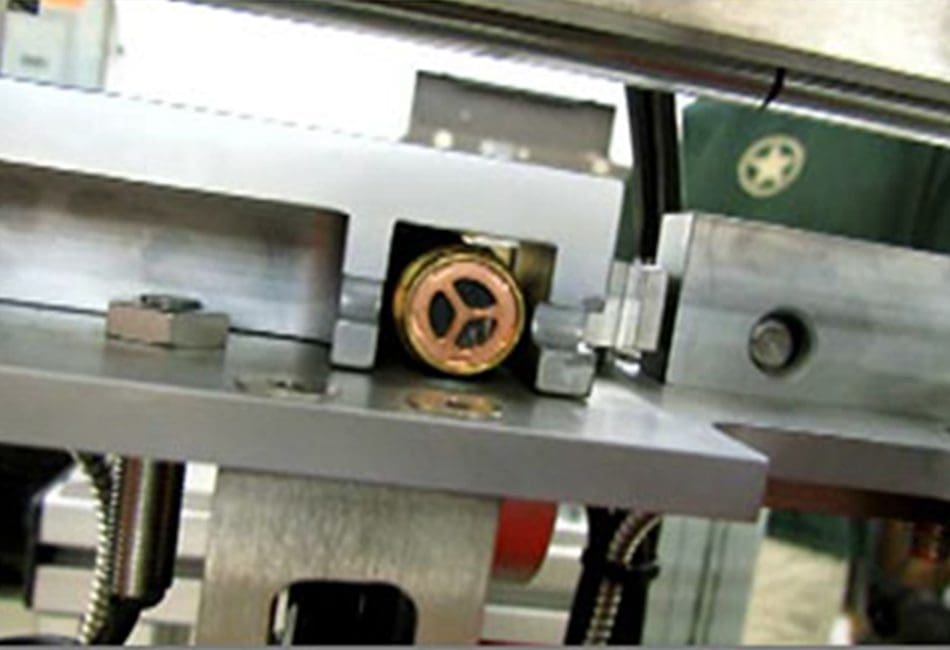
This photo shows a part in the left position of the shuttle after the escapement finger has lowered, allowing the customer’s camera to view the part for inspection.
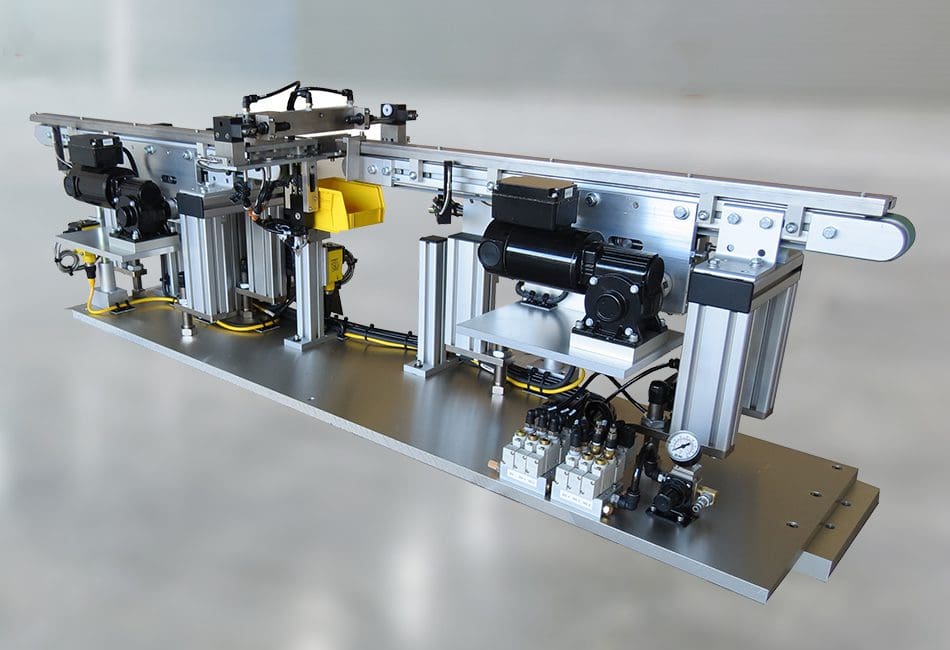
Custom Conveyor System specifications
- Feed rate: 40 parts per minute
- Conveyors (2):
- Auto-Kinetics Model 55 Standard Duty belt conveyors, 40mm wide x 36″ long
- Standard center drive modules, 1/6 HP motors, 130V DC variable speed, with PF-11 DCPM motor controllers (110V AC input)
- Custom part confinement tooling
- Custom table mount stands
- Custom-tooled shuttle mechanism:
- Side shuttle: 3-position pneumatic linear slide with shock absorbers and custom tooling
- Escapement to control part flow from infeed conveyor into shuttle: Pneumatic escapement with custom tooling
- Pusher mechanisms to eject good/bad parts: Pneumatic cylinders with custom tooling
- Sensors and valves provided:
- Air solenoid valve package to supply air to slide, escapement and cylinders
- Photoelectric sensors on each conveyor to detect when the conveyors are full of parts
- Photoelectric sensor on shuttle mechanism to detect when a part is positioned in the shuttle nest
- Proximity sensors (3) to detect shuttle at left (infeed conveyor), center (bad part reject) and right (good part eject to exit conveyor) positions
- Position sensors (2) integrated into escapement to indicate when each finger is extended or retracted
- All sensors and valves wired to terminals in junction box for the customer to interface with their control system
Downloads
Performance Feeders Tri-Fold Brochure
Model 55 Belt Conveyor Product Card