High Speed Vibratory Feeder with Shroud Feeds Medical Parts at 330 Parts Per Minute
Jump to: System Specifications || Quote Request Form ||
This 18-inch vibratory feeder system was designed to orient a plastic medical product component into a vertical position to be received into our customer’s assembly machine.
To support a clean medical assembly process, the system was manufactured to customer specifications with 304 double-welded stainless steel. Part contact areas were ground and electropolished.
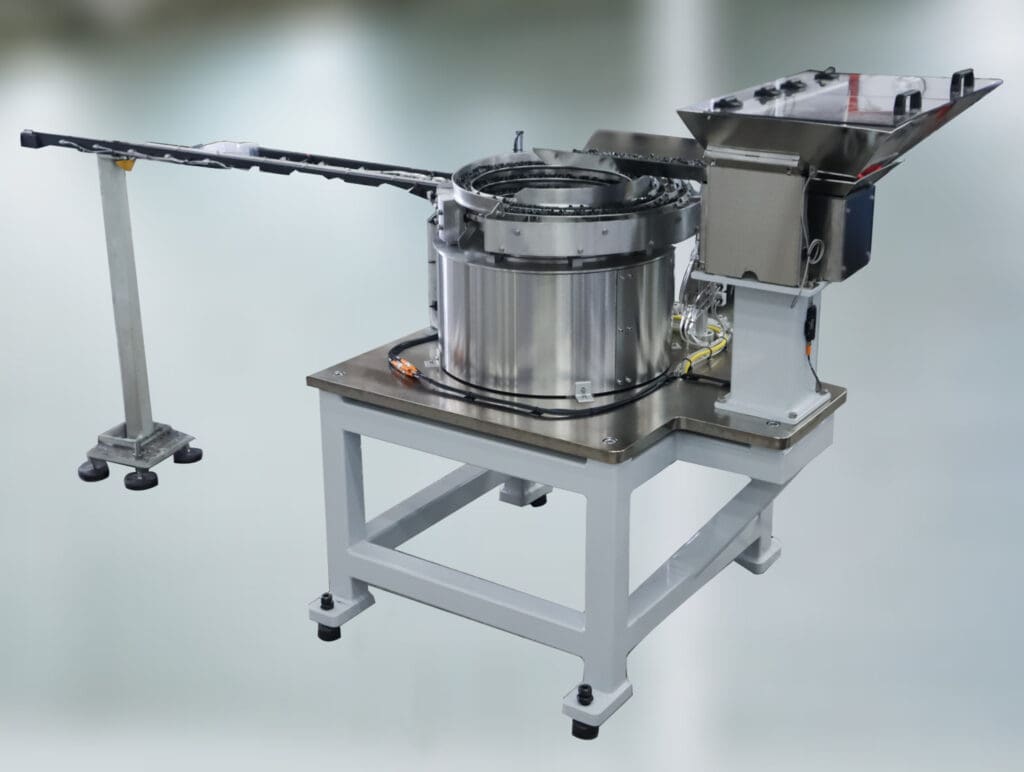
A Lexan lid protected the bulk part supply in the 1 cubic foot stainless steel hopper from environmental particulate.
Part flow from the hopper was regulated using a Keyence sensor. A second Keyence sensor mounted on the hopper bin provided a method to alert the assembly machine’s control system when the level of bulk parts got too low. The customer controlled the system function using REO electronic controls and Turck I/O integration.
A drive unit shroud enclosed the vibratory feeder base, reducing particulate accumulation areas for a sanitary product assembly process and an aesthetically pleasing finish. The vibratory feeder was enclosed in an Alucobond sound enclosure, (not pictured) to reduce noise exposure to a decibel rating of less than 80 DBA.
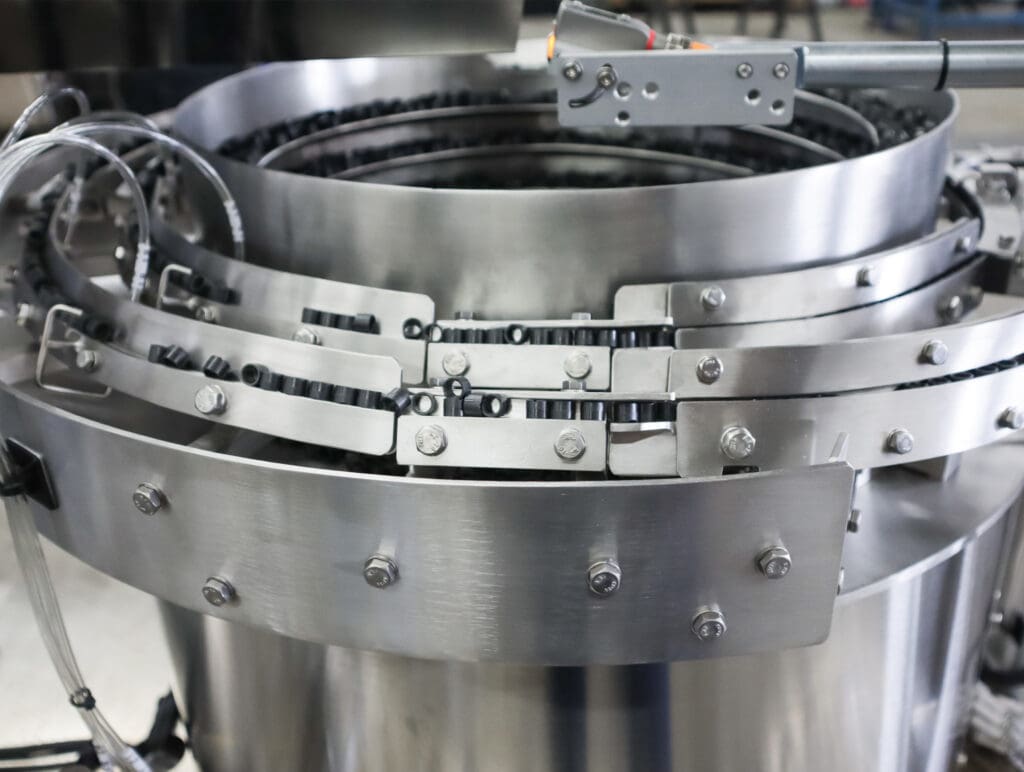
Specifications
- Feed rate: 165 parts per minute, per track (330 parts per minute total output).
- Input voltage: 220V, 50 Hz.
- Vibratory bowl:
- 18″ basic diameter.
- Counterclockwise rotation.
- 304 stainless steel construction, part contact areas ground and doubled welded and electropolished.
- Part contact areas were ground and electropolished.
- Purge gate for part changeover.
- Dual line Compressed Air track:
- Outside track 65.9″ long. Inside track 30.5” long
- Bulk prefeeder:
- Stainless steel construction, contact areas ground and doubled welded and electropolished.
- 1 cu. ft. capacity.
- Lexan lid
- Controls:
- REO electronic controls with Turck I/O integration
,for customer control
- REO electronic controls with Turck I/O integration
- Sensors and valves provided:
- Keyence sensor in the vibratory bowl to regulate part flow
- Keyence sensor mounted on the hopper bin to signal the assembly machine’s control system when the parts level in the hopper was low.
- Sound Enclosure
- Alucobond with silicone seal between enclosure and table top
- Mounting surface: Blanchard ground base plate with leveling pads and locking casters.