This Slant Disc Feeder was designed to feed a plastic medical part. The customer required a low-speed rate of 5 parts a minute and an affordable, cost-effective solution.
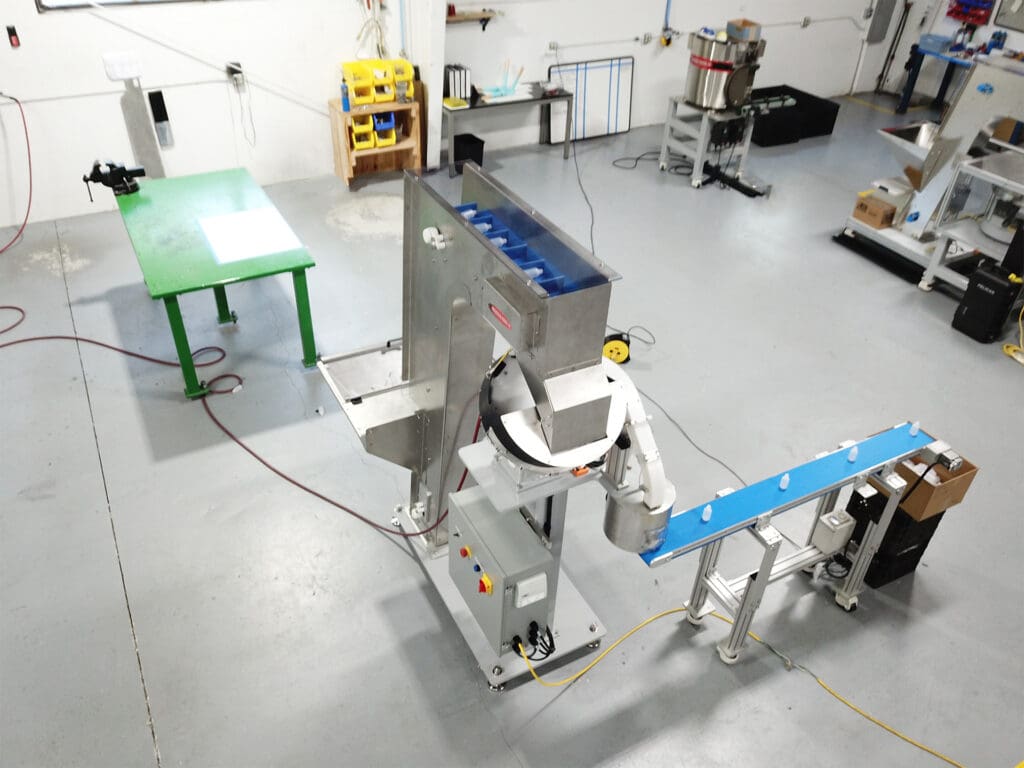
Specifications
- Feed Rate: 5 parts per minute (With capability to feed 60 ppm.)
- Input voltage: 208V, 60 Hz.
- Slant disc feeder bowl:
- 18″ basic diameter.
- Clockwise rotation.
- Teflon coated floors and walls
- Gravity tracking for oriented product
- Star wheel release mechanism:
- 4 pocket star wheel which transferred product from the gravity track to the down stream equipment
- All product contact surfaces are Stainless Steel or FDA compliant materials.
- Bulk supply hopper:
- 3 cu. ft. floor mounted vertical elevator.
- Stainless Steel and FDA compliant materials of construction.
- Controls: Delta Electronics VFD’s and Keyence photo sensors
- Mounting surface: Steel table with heavy duty frame and leveling screws.
- Sensors and valves provided:
- Photoelectric sensors on the bowl to monitor the level of product in the system
- High Level photoelectric sensor on gravity track to turn the slant disc on and off
- Low Level photoelectric sensor on gravity track to turn the star wheel on and off
- Solenoid valve package with regulator and flow controls for air jets.