Reliable Feeding of O-Rings in Vibratory Feeder Bowls
Jump to: System Specifications || Quote Request Form
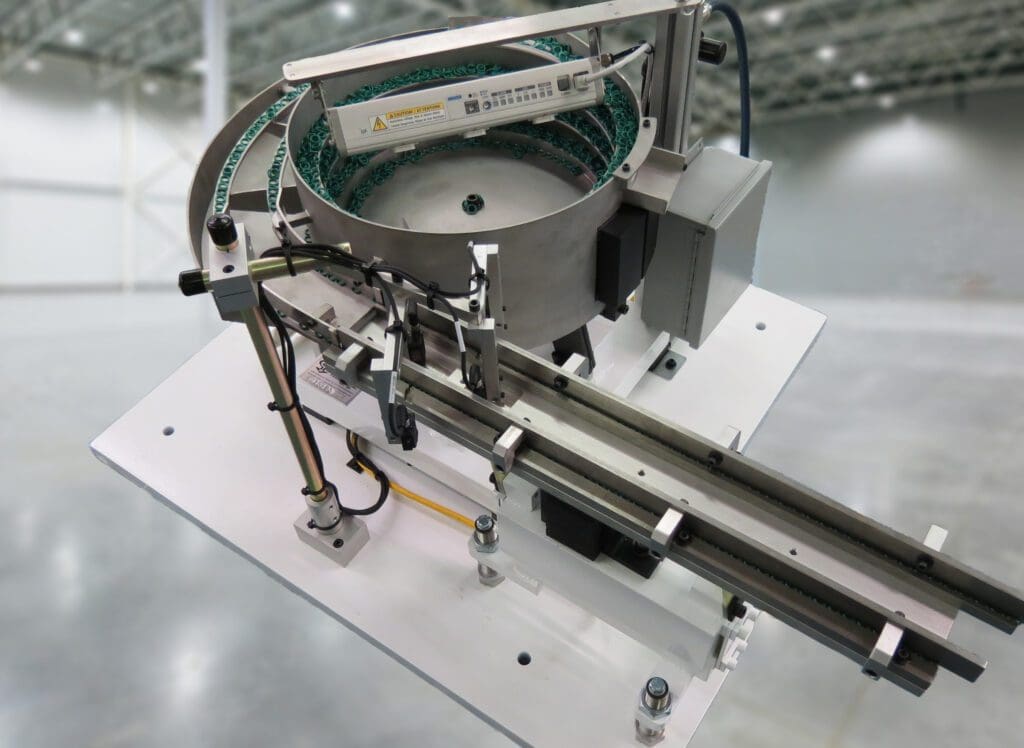
Feeding o-rings in vibratory bowl systems has been historically problematic due to buildup of static electricity causing the parts to stick together and stick to the bowl surface. Coating the parts with talcum powder or baby powder has been a solution in the past, but isn’t acceptable in modern automatic assembly operations, which often feature parts with sensitive electronic components that can’t be contaminated with foreign materials. The clean and dry manufacturing environments these parts are assembled in make the static electricity problem worse.
System specifications
- Feed rate: 30 parts per minute, per line (two lines of parts).
- Input voltage: 220V, 60 Hz.
- Vibratory bowl:
- 15″ basic diameter.
- Counterclockwise rotation.
- Bead blasted stainless steel construction.
- Purge gate that allows for quick part changeover.
- Vibratory straight line track:
- Stainless steel construction.
- Dual-line track mounted to single 2-spring vibratory inline driver.
- Inside track length 24.50″, outside track length 23″.
- Controls: Reovib vibratory feeder controller.
- Ionizer:
- Blows negatively-charged ions into vibratory bowl feeder, dissipating static electricity.
- 24 volt DC power provided by Reovib controller.
- Mounting surface: 1.25″ thick steel plate with mounting holes, sized for future addition of sound enclosure.
- Sensors and valves provided:
- (2) 24 volt DC photoelectric sensors on straight line tracks monitoring the part level. When both lines are full, the bowl is turned off.
- Solenoid valve for ionizer air supply.
Downloads
Performance Feeders Tri-Fold Brochure
Vibratory Feeder Bi-Fold Brochure
Vibratory Feeder Rack Card