What is ‘Industry 4.0’?
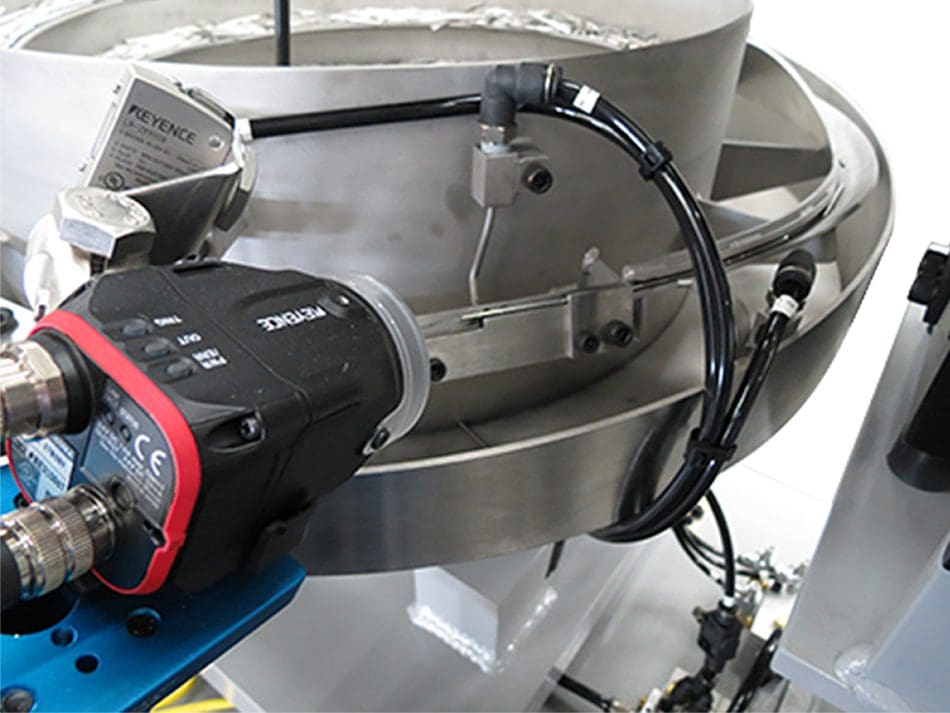
Industry 4.0 or “i4.0” is the next wave of manufacturing, often referred to as ‘smart factories’. i4.0 includes automation and data exchange in manufacturing processes, cyber-physical systems, the Internet of Things (IoT), and cloud computing. According to a recent KPMG report on i4.0 “Gartner believes that the Internet of Things (IoT) market will be worth almost US$3.7 trillion by 2020. Morgan Stanley’s research suggests that the cyber security market (a key prerequisite of i4.0) will be worth around US$183 billion by then. And IDC thinks that the virtual and augmented reality market will be worth US$162 billion. All told, current analyst estimates for the component markets of i4.0 amount to more than US$4.4 trillion by 2020. A massive market, indeed. But, as i4.0 achieves enterprise scale, it will remain to be seen whether business leaders are willing to invest such large sums.”
The race towards i4.0 will not likely be won by companies with the deepest pockets but rather, by those who understand how to use a strategic approach that will create the most value. The key is understanding how i4.0 can be used to simplify process, improve productivity, and reduce time-to-market for products and services. As you begin thinking about integrating technology into your operation, consider that many of your key processes may live only in the heads of your employees. Begin by documenting all processes on your factory floor. This documentation will help you determine where standardization could be improved or new technologies could be integrated. It is especially important to get feedback from your employees as they are the people most familiar with bottlenecks or other production issues that might be effectively addressed with i4.0 technologies.
i4.0 will focus on integrated systems that will be able to track product digitally from order through manufacture and delivery. Customized automation equipment enables manufacturers to produce multiple products using the same equipment which is more efficient and lowers costs. One of the biggest myths surrounding i4.0 is the idea that existing equipment is not capable of communicating with new technologies or that existing legacy or older equipment must be replaced. This is mostly not true – retrofitting equipment to include communication or data collection processes is easier and faster than ever and can begin producing results immediately. For example, adding sensors to monitor the health of your equipment and processes provides both immediate and long-term ROI.
Here are a few steps you can take now to move your manufacturing process towards Industry 4.0:
- Review your future market strategy
- Establish milestones for moving towards i4.0
- Get buy-in from your entire organization around the need to move to a ‘smart factory’
- Plan for addressing any ‘skills gaps’ in your workforce
- Evolve your IT infrastructure
Industry 4.0 is no longer ‘the future’ – it is here and now and only companies with a well-planned and executed strategy to move towards it will survive. What is your organization doing to get ready?